Anodised Aluminium
The aluminium is anodised by the passing of an electrical current from the anode to the cathode. The item to be anodised becomes the anode part of the electrical circuit whilst the cathodes are already in the anodising tank. The electrical current causes oxygen to be released at the anode which combines with the aluminium to form the aluminium oxide which is the anodic film. The depth of the anodic film and colour dyeing is determined by the time in the anodising tank, usually between 15 to 60 minutes which will create an anodic film thickness of between 5 and 25 microns. J57S is the anodising quality grade of Aluminium predominantly used for decorative and architectural applications
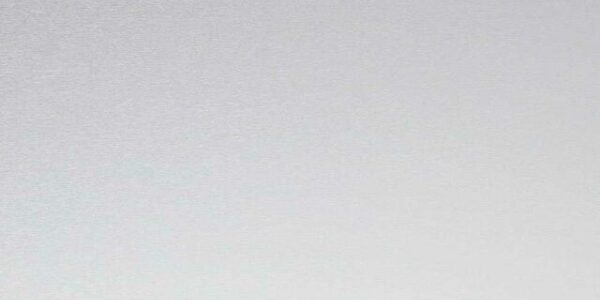
- Natural metallic sheen and aspect
- Excellent corrosion resistance
- Over 30 years of proven long term on-site performance
- No risk of adhesion failure of the anodic film
- No risk of fading
- No risk of chalking
- No risk of filiform corrosion
- Exceptional abrasion resistance
- On-site quality control possible without creating surface damage in testing
- 100% recyclable